Sabe como é uma fábrica de Fórmula 1? Mostramos-lhe a da Renault…
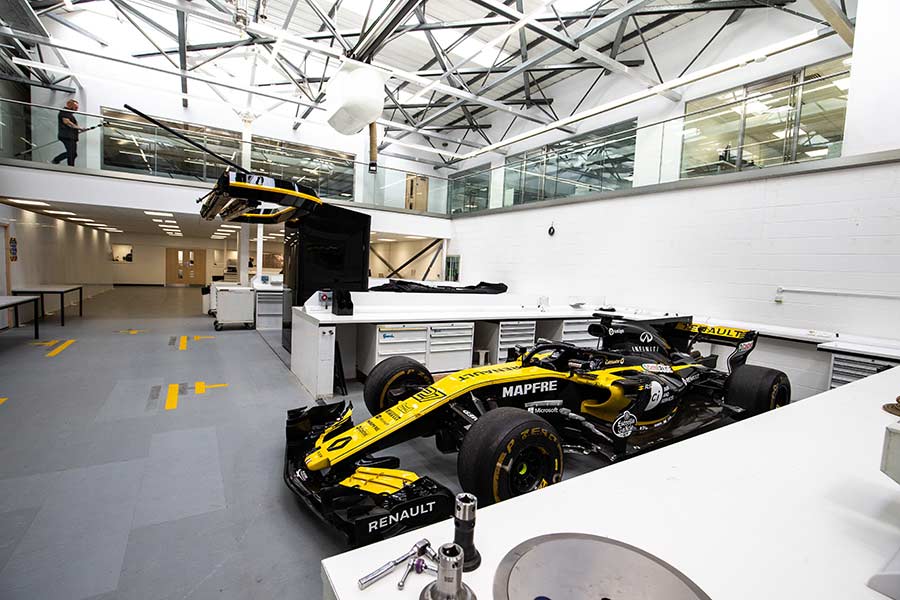
Para ficar a conhecer um pouco melhor a Renault Sport Formula One Team, visitámos a fábrica de Enstone, onde é feito tudo o que diz respeito ao chassis do carro. Desde a sua conceção, aerodinâmica, aspetos dinâmicos do monolugar, design, fabrico de peças compósitas, metálicas, fabricação, montagem e toda a operação de exploração da equipa. O motor é feito em Viry-Chatillon, perto de Paris…
Em Enstone existe um túnel de vento para um modelo com a escala (máxima obrigatória) de 60%, com toda a parafernália adjacente de visualização e análises técnicas, um simulador, dos mais evoluídos que existem no mercado, uma sala de operações totalmente ligada às boxes da equipa nas pistas.
Desde que a Renault chegou a Enstone, os números de pessoal cresceram 50%, sendo que neste momento trabalham ali 680 pessoas de 22 nacionalidades. Até ao final do próximo ano deverão estar em Enstone cerca de 750 pessoas. Tudo somado, a operação de F1 da Renault ascende neste momento a mais de 300 milhões de euros/ano.
Investimentos em Enstone
Desde janeiro de 2016, foram feitos investimentos em Enstone de mais de 50 milhões de euros. A fábrica foi ampliada e cerca de 2000m², isto para além de uma extensiva renovação e reajustamento do que existia. A fábrica foi dotada de novos modernos equipamentos, que aumentou exponencialmente a capacidade de produção da fábrica. Foram adquiridas 20 novas máquinas CNC (Computer Numerical Control, máquinas eletro mecânicas, que geram protótipos de peças a partir de um ficheiro informático), seis máquinas ADM (que permitem uma grande customização no fabrico de peças, que não era possível na manufaturação), um novo cluster de CFD (em inglês: Computational Fluid Dynamics, Simulação computacional).
Foi adquirido também um novo dinamómetro (útil no desenvolvimento e preparação de motores). Foi ainda feito um grande ‘upgrade’ ao túnel de vento, construída uma nova área de pintura, um banco de ensaios de chassis. Foi também duplicada a área da ‘clean room’, local onde se fabricam todos os componentes compósitos.
Plano a seis anos
A Renault Sport Fórmula 1 Team está neste momento no seu terceiro ano de seis previstos para esta fase de desenvolvimento da equipa e para 2019, como já é público a maior novidade passou pela contratação de um piloto de topo, Daniel Ricciardo, que se junta em 2019 a Nico Hulkenberg, o que em teoria significa que só neste aspeto a equipa possa elevar o seu nível.
Ao trabalhar numa estrutura como a da Red Bull há largos anos, o australiano tem uma compreensão muito grande do que é preciso para vencer, e o simples facto de exigir um carro e uma equipa à altura do seu talento, poderá fazer com que todos os que gravitam à volta de uma equipa de F1 elevem o seu nível.
O que vemos em pista é claramente diretamente proporcional ao trabalho combinado das muitas centenas de pessoas que trabalham em Enstone e Viry-Chatillon, e Ricciardo é mais uma peça que pode ajudar a olear toda esta complexa engrenagem.
A plataforma existente já é sólida, mas para chegar onde quer, a Renault tem que aprimorar todo o seu trabalho, pois só com isso consegue mais performance e consequentemente reduzir a margem para as três equipas da frente, Mercedes, Ferrari e Red Bull.
Para o ano, o quarto deste plano a seis anos, é intenção dos responsáveis da equipa, lutarem por pódios, talvez ainda não com muita consistência, mas começarem a aparecer por lá perto. Mas para isso têm, logicamente, que se afastar claramente do meio do pelotão, o que conseguiram na segunda metade desta época, mas que neste momento têm tido dificuldades em manter.
Desde a primeira corrida da Renault na F1 em 1977, passando pelos anos 90, uma era de domínio ‘motorizado’ através da Williams e Benetton, os bem sucedidos mundiais de 2005 e 2006 já como construtor, um novo período de domínio como fornecedor de motores, entre com a Red Bull Racing, entre 2010 e 2013, este mais recente capítulo surge com objetivos ambiciosos, mas como já se percebeu há muito, a concorrência é muito forte, está para já ainda longe, e vai levar tempo para lá chegar.
Quanto, é difícil dizer, mas fica a certeza que o trabalho que está a ser feito vai dar frutos, pois não faltam recursos, instalações e gente capaz de ‘entregar’ resultados. O foguete arrancou, está a ganhar embalo, olhando para os resultados, o crescimento tem sido evidente, mas agora faltam os degraus mais difíceis de todos, os que levam à ‘penthouse’, onde estão instaladas as super-equipas.
Neste momento, em termos de estrutura humana e material, o que separa a Mercedes, Ferrari e Red Bull da Renault já não é expressiva, mas todos os departamentos da Renault na F1 têm agora que elevar ainda mais o seu nível. Para perceber um pouco melhor o que se tem vindo a fazer em Enstone, siga as próximas páginas…
História de Enstone
Enstone tem sido a casa de equipas de F1 desde 1992. Depois de comprar a Toleman, a Benetton a Renault comprou a fábrica aos italianos em 2000, cinco anos depois venceu o Mundial de F1, entre 2011 e 2015, a equipa passou a chamar-se Lotus Renault GP e depois Lotus F1 Team, até que a anunciou que regressaria à F1 como equipa de fábrica no final de 2015. Enstone é o coração da operação de chassis da equipa, num trabalho supervisionado pelo Diretor Executivo, Marcin Budkowski e o Diretor Técnico de Chassis, Nick Chester.
Design Office
Numa sala onde se vive e respira Renault F1, a maioria dos cerca de 70 funcionários, está vestido com a camisola do ‘clube’, há réplicas à escala dos F1 espalhados pelas secretárias, nem os fundos de ecrã escapam…
Desenhar um F1 é uma tarefa extremamente complexa e detalhada, com um enorme conjunto de fatores que têm de ser levados em conta, quer seja no design, quer no processo de implementação. Só para o desenho do chassis, em Enstone, são designadas mais de 70 pessoas, no Design Office (DO). Desenho da transmissão, mecânica, análises de stress, por exemplo. O Vehicle Performance Group (VPG) é outro grupo, cujo propósito é desenvolver um plano que encoraja a interação entre os diversos sub grupos, para que tudo se ‘ligue’.
São gastas cerca de 150.000 horas, feitos 19.000 desenhos assistidos por computador (CAD, Computer Aided Design) para definir 14.500 componentes do carro, com o trabalho a começar cerca de 18 meses antes do arranque da época a que esse monolugar diz respeito. Todos os anos, a FIA determina os regulamentos, que são depois totalmente escrutinados pela gestão da equipa e designers, de modo a afinarem os seus planos iniciais e tornarem o conjunto o mais competitivo possível.
Doze meses antes do arranque da época, o desenho do monolugar já está a ser feito, e os primeiros componentes são testados. Oito meses antes do início da época, começa o trabalho no túnel de vento. O primeiro chassis tem que estar pronto antes do Natal.
Contudo, é sempre um equilíbrio difícil de conseguir, pois evoluir o monolugar que está a correr nesse momento é igualmente importante, e os resultados (ou a falta deles) determinam normalmente para onde vai o foco. No ano a seguir ou no atual. E esta é uma decisão crítica, pois apostar no atual pode contribuir para que o próximo… falhe.
Túnel de Vento e CFD
A F1 é um desporto em que a aerodinâmica desempenha um papel muito importante e isso reflete-se no tamanho e na importância da equipa de Aerodinâmica em Enstone. O túnel de vento tem um papel fundamental no design, desenvolvimento e compreensão aerodinâmica de um monolugar de Fórmula 1. O túnel de vento de Enstone foi inaugurado em 1998, ocupa 2.674 m² sendo que ao contrário do passado, a sua atividade é restrita e totalmente controlada pela FIA. A federação em qualquer momento pode solicitar a gravação de uma ou mais sessões, existem câmaras ligadas à FIA, que olha para elas quando quer.
Desde 2014 e por motivos de controlo de custos, as equipas só podem operar 520 vezes o túnel de vento num período de oito semanas, o que equivale a cerca de 65 sessões por semana. Pode fazer mais ou menos, mas o total não pode ser ultrapassado, sob pena de fortes multas. A FIA verifica e regista todas as atividades das equipas no túnel de vento, de modo a policiar essa regra.
A FIA obriga também a utilização de um modelo à escala, de 60%, no máximo, que é colocado no tapete rolante do túnel de vento, onde é exposto a uma velocidade restrita a 50 metros por segundo (180 Km/h). Todo e qualquer componente pode ser testado, e com isso determinado o seu potencial. Todos os elementos que afetam o carro, são testados no túnel de vento. Basta olhar-se para um F1 atual e perceber a quantidade de peças e pequenas asas que podem ser utilizadas. São testadas cerca de 250 peças por semana, mas com uma velocidade máxima pré-determinada de 180 Km e um modelo com uma escala de 60% nunca os engenheiros terão os resultados que gostavam. Para além disso o túnel de vento só ‘lê’ o monolugar a direito e não em curva, onde é mais necessário que a aerodinâmica faça o seu trabalho.
No túnel de vento é possível testar a aerodinâmica, altura ao solo, drag, deformação dos pneus e o sistema de escape. Em 2017, o túnel de vento foi melhorado e recebeu um sistema de tapete rolante tendo sido também aumentado o ângulo de ‘guinada’.
Departamento de Produção
Mais de 90% do chassis é produzido em Enstone. O departamento de fabrico é responsável pelos radiadores e escapes, entre outras peças menores. Apesar da necessidade de alta precisão, neste caso ainda não há melhor maneira do que fazer as peças manualmente. O sistema de escape, em particular, é super detalhado, pois varia em espessura de 1,1 mm a 0,3 mm na saída. Confirme vai ‘arrefecendo’, menor a espessura…
O ‘Compósitos’ é um dos maiores departamentos de Enstone, com mais de 50 pessoas. É formado por modeladores, laminadores e montadores. O peso mínimo de um monolugar de F1, é de 734 kg pelo que o objetivo da equipa de compósitos é fazer com que o carro seja o mais leve possível.
Mas com isso tem sempre que se ter em conta a segurança, pelo que toda e qualquer nova peça, ‘inventada’ pela mistura de materiais compósitos tem de passar por várias avaliações e testes de colisão, e há parâmetros que têm de ser cumpridos.
É assim, estando constantemente a estudar como tornar as 14.500 peças do carro mais leves, que se chega a um ponto em que pode ser adicionado lastro ao carro, de modo a que atinja o peso limite legal, sendo que isso dá aos engenheiros valiosa ‘latitude’ para otimizar o centro de gravidade do carro.
A equipa usa grandes quantidades de fibra de carbono por temporada, cerca de 18 km de extensão por um metro de largura. A fibra de carbono é duas vezes mais forte que o aço, e cinco vezes mais leve, e contribuiu muito para aumentar a segurança da F1 nas últimas duas décadas.
As peças de metal de um F1 são feitas na oficina de mecânica, uma instalação de última geração em que as peças são feitas de metais leves e fortes, como titânio, alumínio e Inconel (é uma liga de níquel e alumínio que resiste a altas temperaturas em ambientes extremos.
Foi originalmente desenvolvida pela Rolls-Royce para motores a jato, e depois tornou-se vital na indústria motorizada, por exemplo nos escapes dos Renault de F1).
Algumas das mais avançadas tecnologias de maquinação são usadas e permitem que a equipa produza mais de 50.000 componentes de metal para os carros, durante uma temporada. As máquinas estão em quase constante funcionamento.
Em Enstone existem cerca de 20 máquinas CNC (computer numerical control), EDM (electrical discharge machining) e GF (para peças de alta precisão), 90% das quais foram renovadas no último ano. O processo de fabricação de um chassis pode levar até cinco semanas de trabalho. A precisão dessas máquinas economiza 30% em tempo, quando comparadas com as suas antecessoras.
Eletrónica
Existem centenas de componentes eletrónicos num F1. Os mais visíveis estão no volante, mas debaixo da ‘pele’ há centenas de sensores que fornecem dados críticos para a equipa, e controlam os complexos sistemas de um carro. Os sensores fornecem uma parte crucial da informação, desde a temperatura dos travões, até à ‘forma’ dos sistemas do motor. A aquisição de dados é fundamental para a análise em tempo real e para o desenvolvimento do conjunto. Qualquer informação pode redundar numa alteração de uma peça cujos sensores ‘informaram’ que estava a funcionar fora dos parametros estabelecidos.
Os dados são projetados e produzidos em Enstone, sendo que o departamento de Eletrónica, composto por 21 pessoas, oito engenheiros, sete elementos da produção, quatro na equipa de corridas, e dois na equipe de testes.
Banco ensaio chassis
Rene Torcato é o responsável por um departamento onde se testa a performance dos carros através da suspensão. Usam a plataforma de sete pontos para desenvolver novas configurações de suspensão para o carro, procurando novas ideias para a suspensão antes de rumarem à pista. Basicamente colocam um chassis em 17 atuadores servo-hidráulicos, que replicam as forças que o carro sofre na pista. Há catorze atuadores sob as rodas, que aplicam forças verticais e horizontais, e outras três sob o piso para replicar as forças aerodinâmicas.
As voltas gravadas anteriormente são passadas para o novo chassis, depois testam-se diversas configurações de molas, amortecedores, e os sensores registam toda a informação, a força que é exercida sobre os diversos componentes do carro, e isso faz-se com cerca de cinco corridas de avanço, sendo que dali saem informações valiosas quanto à forma como o carro é afinado de base. Deste modo, em termos de chassis o carro chega a cada pista com uma afinação base, e nos treinos livres os pilotos fazem o ‘fine tunning’, adequando o carro o melhor possível aos pneus, peso, tendo em conta o combustível, etc.
Simulador
O simulador desempenha um papel crítico no desenvolvimento de um F1 e é de grande utilidade não apenas para os pilotos, mas também para os engenheiros, projetistas e o Grupo de Desempenho (VPG). A instalação da Enstone foi encomendada em 2011 com o modelo do carro projetado pela equipa. Os mapas e circuitos são fornecidos pelo conhecido programa R Factor Pro. O simulador de Enstone possui cinco projetores principais de alta definição, e o motor do simulador fornece uma representação o mais realística possível das forças geradas pelo carro. A telemetria é precisa tendo em conta o que é vivido em pista e fornece dados muito úteis aos pilotos e engenheiros na preparação para uma corrida.
Sala de Operações
Quando arranca a primeira sessão de treinos livres de um qualquer Grande Prémio, seja a que horas ‘europeias’ for, Enstone está a fervilhar de gente e a Sala principal é mesmo a de Operações.
A boa comunicação entre esta sala e o circuito é essencial, há diversos canais e uma estrutura muito bem definida de quem fala com quem. Os pilotos só falam com duas ou três pessoas no máximo, o seu engenheiro, e duas no muro das boxes.
Durante um fim de semana de corrida, membros da equipa de VPG (Vehicle Performance Group), estratégia de corrida, aerodinâmica, informática, e IS (suporte) são estrategicamente colocados nas suas áreas de trabalho para monitorizar os dados relativos à sua área e com isso garantir o melhor nível de comunicação entre as pessoas certas.
Existem mais de 200 sensores nos carros, que fornecem 150.000 medições por segundo, registam temperaturas, pressões, acelerações, entre muitas outras coisas. Os dados surgem em tempo real e por vezes estes elementos sabem que algo vai suceder ao ‘seu’ piloto, pois a transmissão tem um delay de cerca de 10 segundos, ou mais, e os dados a que têm acesso são instantâneos, ou para ser mais preciso, demoram 0,25 segundos a chegar a Enstone.
As informações são usadas durante todo o fim de semana de Grande Prémio, para avaliar possíveis problemas com o carro, prever estratégias, melhorar as reações a uma série de cenários que estão em constante evolução, e esta equipa olha para todos os detalhes possíveis e imaginários, faz simulações de estratégias. Têm acesso a todos os tempos, live GPS, TV, webcams, telemetria.
NOTA: Vídeo feito antes do início da época de 2017
Já não é mais possível o Autosport continuar a disponibilizar todos os seus artigos gratuitamente.
Para que os leitores possam contribuir para a existência e evolução da qualidade do seu site preferido, criámos o Clube Autosport com inúmeras vantagens e descontos que permitirá a cada membro aceder a todos os artigos do site Autosport e ainda recuperar (varias vezes) o custo de ser membro.
Os membros do Clube Autosport receberão um cartão de membro com validade de 1 ano, que apresentarão junto das empresas parceiras como identificação.
Lista de Vantagens:
-Acesso a todos os conteúdos no site Autosport sem ter que ver a publicidade
-Oferta de um carro telecomandado da Shell Motorsport Collection (promoção de lançamento)
-Desconto nos combustíveis Shell
-Acesso a seguros especialmente desenvolvidos pela Vitorinos seguros a preços imbatíveis
-Descontos em oficinas, lojas e serviços auto
-Acesso exclusivo a eventos especialmente organizados para membros
Saiba mais AQUI